Real Tips About Which Is Better IR Sensor Or Ultrasonic
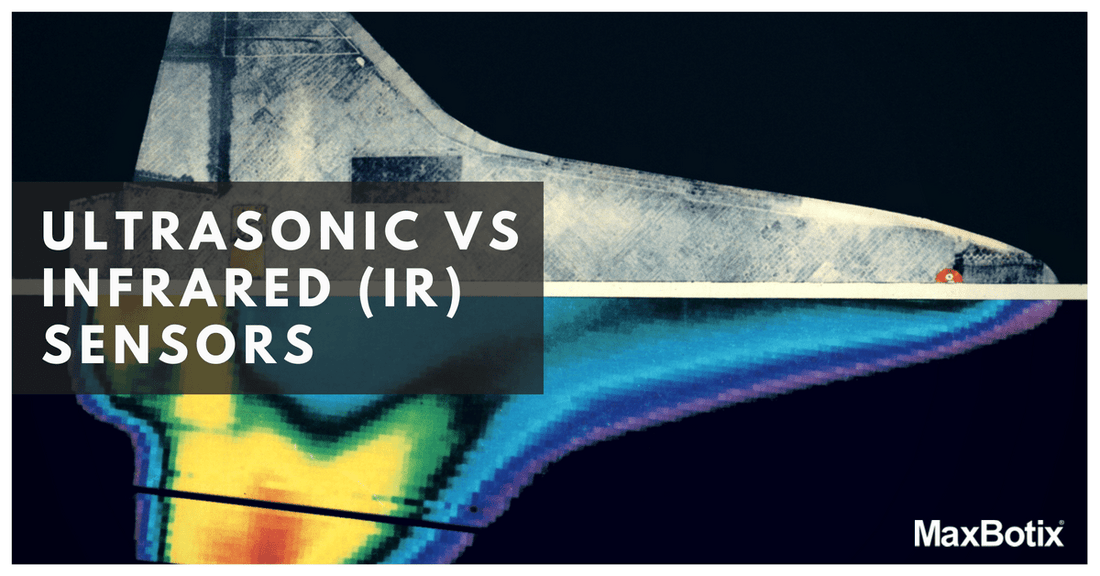
Sensing the Situation
1. Understanding the Basics
So, you're diving into the world of sensors, huh? Smart move! They're everywhere, from your automatic doors at the grocery store to your robot vacuum cleaner. But with so many options, picking the right one can feel like trying to choose between pizza and tacos — both are good, but they serve different purposes! Today, we're tackling two popular contenders: the IR (infrared) sensor and the ultrasonic sensor. Let's break down their strengths and weaknesses to help you make an informed decision. It's not about one being inherently "better," but rather which one is better for your specific application. Think of it like choosing the right tool for the job — you wouldn't use a hammer to screw in a nail, would you? (Okay, maybe you would, but it wouldn't be very efficient!)
At its core, an IR sensor detects infrared radiation. Everything emits infrared radiation, and the amount and wavelength depend on the object's temperature. IR sensors can be passive, detecting existing infrared radiation, or active, emitting their own beam and measuring the reflection. Think of it as a tiny, heat-sensitive eye. Ultrasonic sensors, on the other hand, work by emitting sound waves at a frequency above human hearing (hence "ultrasonic"). They then measure the time it takes for the sound waves to bounce back, allowing them to calculate the distance to an object. Imagine it as a tiny sonar system, sending out "pings" and listening for the echo.
These sensors are everywhere. IR sensors are often found in remote controls (think channel surfing on your couch!), motion detectors, and even some medical devices. They are relatively inexpensive and simple to implement. Ultrasonic sensors are commonly used in parking sensors on cars, level sensors in tanks, and robot navigation systems. Their ability to accurately measure distance makes them ideal for applications where precision is key. Essentially, one "sees" heat, while the other "hears" echoes. Now, the real question: which one is your new best sensor friend?
Don't worry, we'll get into all the juicy details, comparing their accuracy, range, sensitivity to environmental factors, and cost. We'll also explore real-world examples to show you where each sensor truly shines. By the end of this, you'll be a sensor selecting pro!
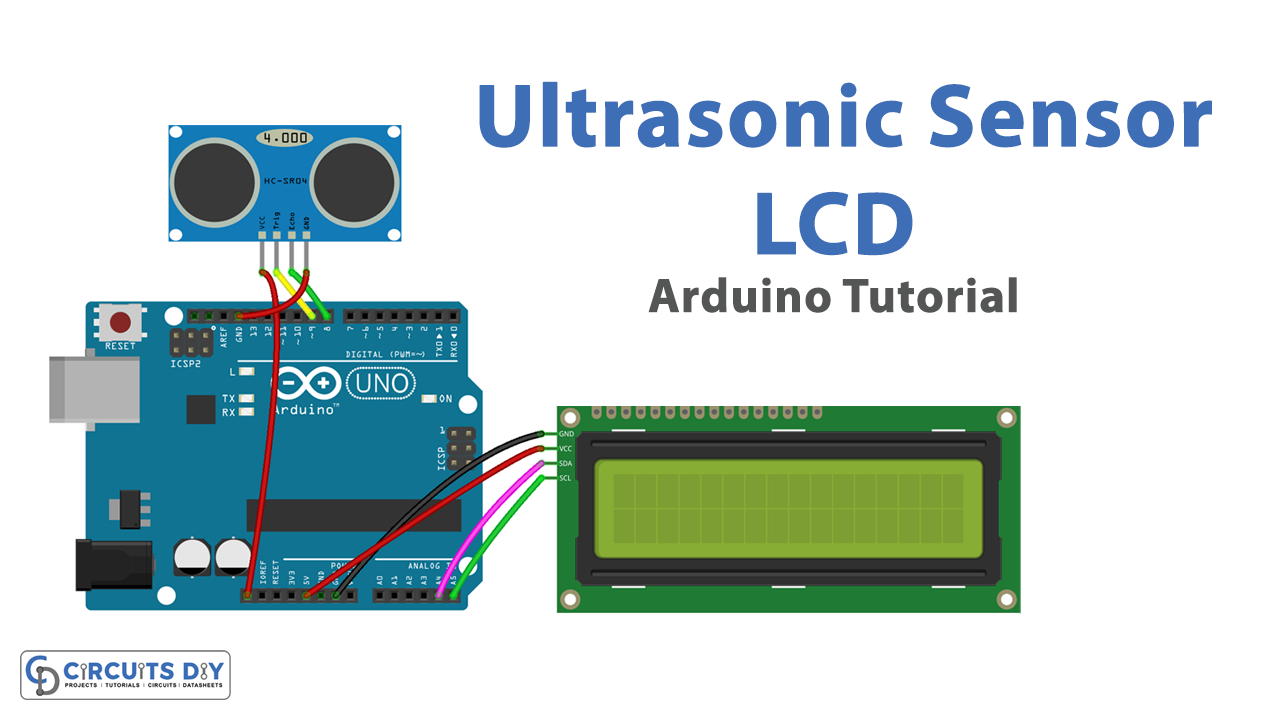
Accuracy Face-Off
2. Precision Matters
When it comes to sensors, accuracy is paramount. No one wants a robot vacuum that constantly bumps into walls or a parking sensor that tells you you're clear when you're about to kiss the bumper of the car behind you. So, how do our IR and ultrasonic contenders stack up in the accuracy department? Generally, ultrasonic sensors tend to be more accurate, especially when measuring distance. They can provide relatively precise measurements, making them suitable for applications requiring accurate spatial awareness. However, accuracy is also influenced by things like temperature and the surface characteristics of the object being detected.
IR sensors, especially simpler ones, often struggle with accuracy, particularly over longer distances. Their readings can be influenced by ambient temperature, the color and reflectivity of the object, and even the presence of other infrared sources. Imagine trying to detect a warm object against a backdrop of other warm objects it's like trying to find a specific grain of sand on a beach! However, more advanced IR sensors, especially those using thermal imaging techniques, can achieve impressive accuracy, but at a higher cost. These fancy IR sensors are used in applications like medical diagnostics and building inspections, where precise temperature measurements are crucial.
Think of it this way: if you need to measure the exact distance to an object with high precision, ultrasonic is likely the better choice. But if you just need to detect the presence of an object or a general temperature difference, a simpler IR sensor might suffice. For example, if you're designing a robot that needs to navigate a complex environment without bumping into anything, ultrasonic sensors would be essential. But if you're building a simple alarm system that detects motion in a room, an IR sensor might be perfectly adequate.
It's also important to consider the specific model of each sensor. Just like cars, sensors come in different models with varying levels of performance. So, always check the sensor's specifications and read reviews before making a decision. Don't just assume that all IR sensors are inaccurate or that all ultrasonic sensors are precise! Remember, choosing the right sensor is all about matching its capabilities to the specific requirements of your project.

Ir Sensor Vs Ultrasonic What Is The Difference Artofit
Range and Sensitivity
3. Distance and Detection Capabilities
The range and sensitivity of a sensor dictate how far it can detect an object and how sensitive it is to changes in its environment. These factors are crucial depending on the application. For instance, a parking sensor needs a shorter range than a drone's obstacle avoidance system. Now, let's see how our IR and ultrasonic sensors fare in this arena.
Ultrasonic sensors typically have a longer range than basic IR sensors. They can detect objects several meters away, making them suitable for applications like parking assistance systems and robot navigation. However, their range can be affected by factors like air temperature and humidity, which can alter the speed of sound. Additionally, the shape and surface of the object being detected can also influence the range. A smooth, hard surface will reflect sound waves more effectively than a soft, irregular surface.
Basic IR sensors, on the other hand, usually have a shorter range, often limited to a few meters. However, they can be highly sensitive to changes in infrared radiation, making them ideal for detecting motion or temperature differences. Specialized IR sensors such as thermal cameras can have a very long range for detecting heat signatures but are much more expensive. Their effectiveness can be affected by ambient light, obstructions, and the object's surface characteristics.
Choosing between the two depends on the needs of the applications. For example, an autonomous robot navigating a warehouse would benefit from the longer range of ultrasonic sensors, while a security system designed to detect human presence might do just fine with an IR sensor's shorter range and high sensitivity to changes in body heat. Therefore, consider the environment where the sensor will operate and the characteristics of the objects it needs to detect.
In summary, when long-range detection is required, ultrasonic sensors are generally the better choice. However, for applications needing high sensitivity to changes in heat or motion over a shorter distance, IR sensors often offer a more effective and cost-efficient solution. Always consider the trade-offs to select the optimal sensor for your particular use case.
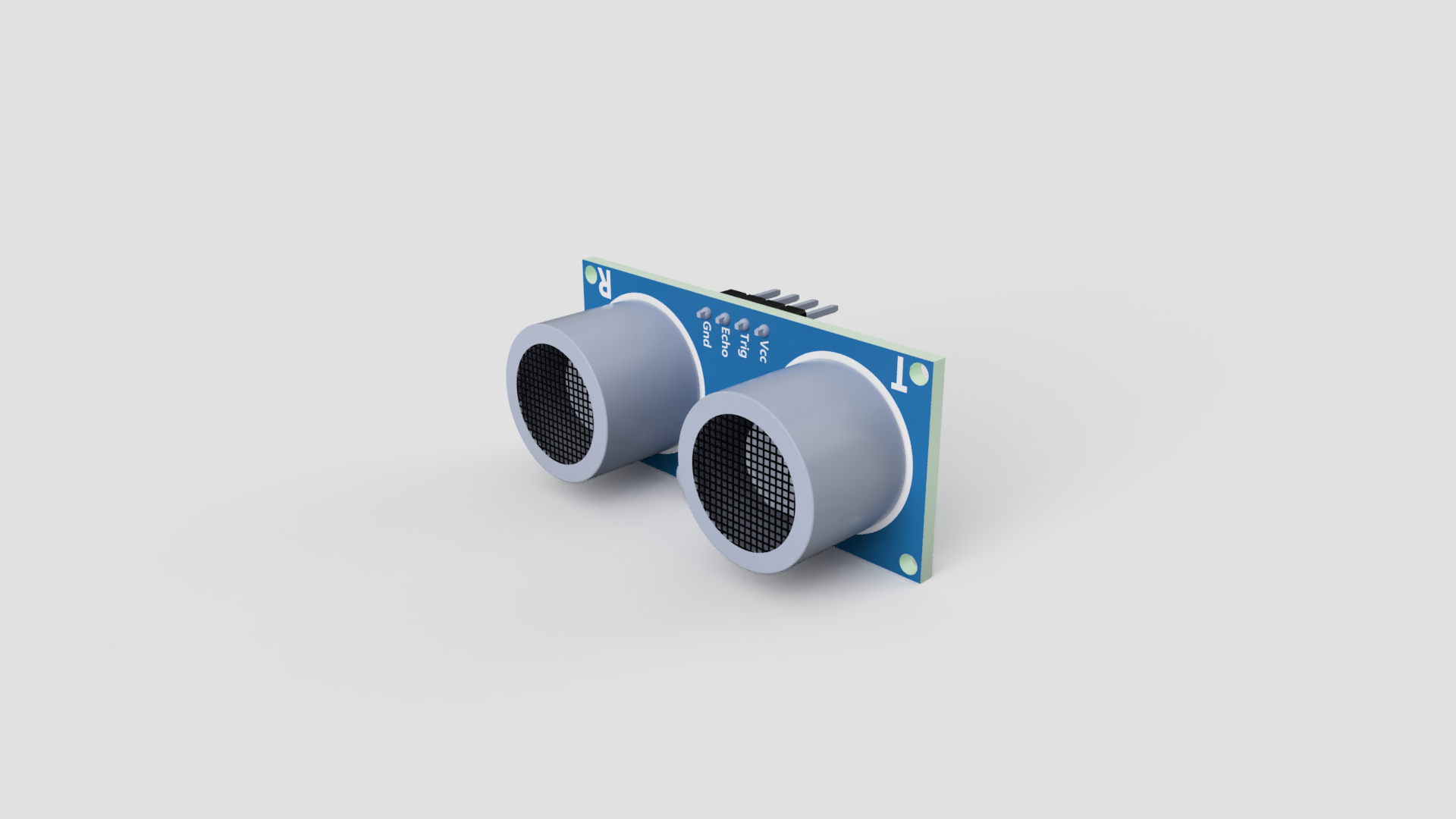
Ultrasonic Sensors
Environmental Factors and Cost
4. Considering the Practicalities
Beyond accuracy and range, environmental factors and cost play a significant role in selecting the right sensor. No sensor operates in a vacuum (unless it's in space, of course!). Temperature, humidity, light, and even dust can all impact a sensor's performance. And, of course, the price tag is always a consideration, especially when dealing with budget constraints. So, let's dive into the practicalities of using IR and ultrasonic sensors.
IR sensors are particularly susceptible to environmental conditions. Sunlight, for example, emits a significant amount of infrared radiation, which can interfere with an IR sensor's readings. Temperature fluctuations can also affect their accuracy, as the sensor might misinterpret changes in ambient temperature as changes in the target object's temperature. Dust and other particles can also block the infrared radiation, reducing the sensor's range and effectiveness. Therefore, IR sensors are generally better suited for indoor environments or applications where environmental conditions are relatively stable.
Ultrasonic sensors are less affected by light and temperature changes compared to IR sensors. However, they are sensitive to humidity and air pressure, which can affect the speed of sound and thus the accuracy of distance measurements. In dusty or noisy environments, the sound waves emitted by the sensor can be scattered or absorbed, reducing its range and accuracy. However, there are specialized ultrasonic sensors designed for harsh environments, which are often sealed and more robust. This makes them better suited for outdoor or industrial applications.
In terms of cost, basic IR sensors are generally cheaper than ultrasonic sensors. This makes them an attractive option for cost-sensitive applications like simple motion detectors or remote controls. However, more advanced IR sensors, especially thermal imaging cameras, can be quite expensive. Ultrasonic sensors, while typically more expensive than basic IR sensors, offer better accuracy and range in many applications, making them a worthwhile investment in the long run. It's always a balancing act between cost, performance, and reliability.
So, when choosing between IR and ultrasonic sensors, consider the environment where the sensor will operate, the budget constraints, and the required level of performance. If you need a simple, low-cost solution for indoor use, an IR sensor might be sufficient. But if you need higher accuracy and reliability in a more challenging environment, an ultrasonic sensor might be the better choice. Don't forget to factor in the long-term cost of maintenance and replacement as well!

Real-World Applications
5. Putting Them to Work
Okay, enough theory! Let's see these sensors in action. Understanding how IR and ultrasonic sensors are used in real-world applications can help you visualize their strengths and weaknesses and make a more informed decision for your own projects. From consumer electronics to industrial automation, these sensors are quietly working behind the scenes, making our lives easier and more efficient.
IR sensors are commonly used in remote controls for TVs, air conditioners, and other electronic devices. They are also found in motion detectors for security systems, where they detect changes in infrared radiation caused by a moving person or object. In the medical field, IR sensors are used in thermometers to measure body temperature without contact. They're also in line-following robots, and even in some basic collision avoidance systems for lower-cost applications. Their simplicity and low cost make them ideal for applications where high accuracy isn't critical.
Ultrasonic sensors, on the other hand, are widely used in parking sensors in cars, where they measure the distance to nearby objects and alert the driver to potential collisions. They are also used in liquid level sensors in tanks, where they monitor the level of liquid without coming into contact with it. In robotics, ultrasonic sensors are used for obstacle avoidance and navigation, allowing robots to move safely through complex environments. They are also in industrial applications, such as detecting the presence of objects on a conveyor belt or measuring the distance to a target in a manufacturing process.
Consider a self-driving car. It uses a combination of sensors, including ultrasonic and more advanced technologies like LiDAR, to navigate its environment. Ultrasonic sensors can be used for short-range object detection, while LiDAR provides a more detailed 3D map of the surroundings. Or take a smart home system: IR sensors can be used to control lights and appliances, while ultrasonic sensors can be used to detect the presence of people in a room and adjust the temperature or lighting accordingly.
Ultimately, the choice between IR and ultrasonic sensors depends on the specific application and the desired level of performance. By understanding their strengths and weaknesses and seeing how they are used in real-world scenarios, you can make the best decision for your own projects. Now go forth and sense the world!
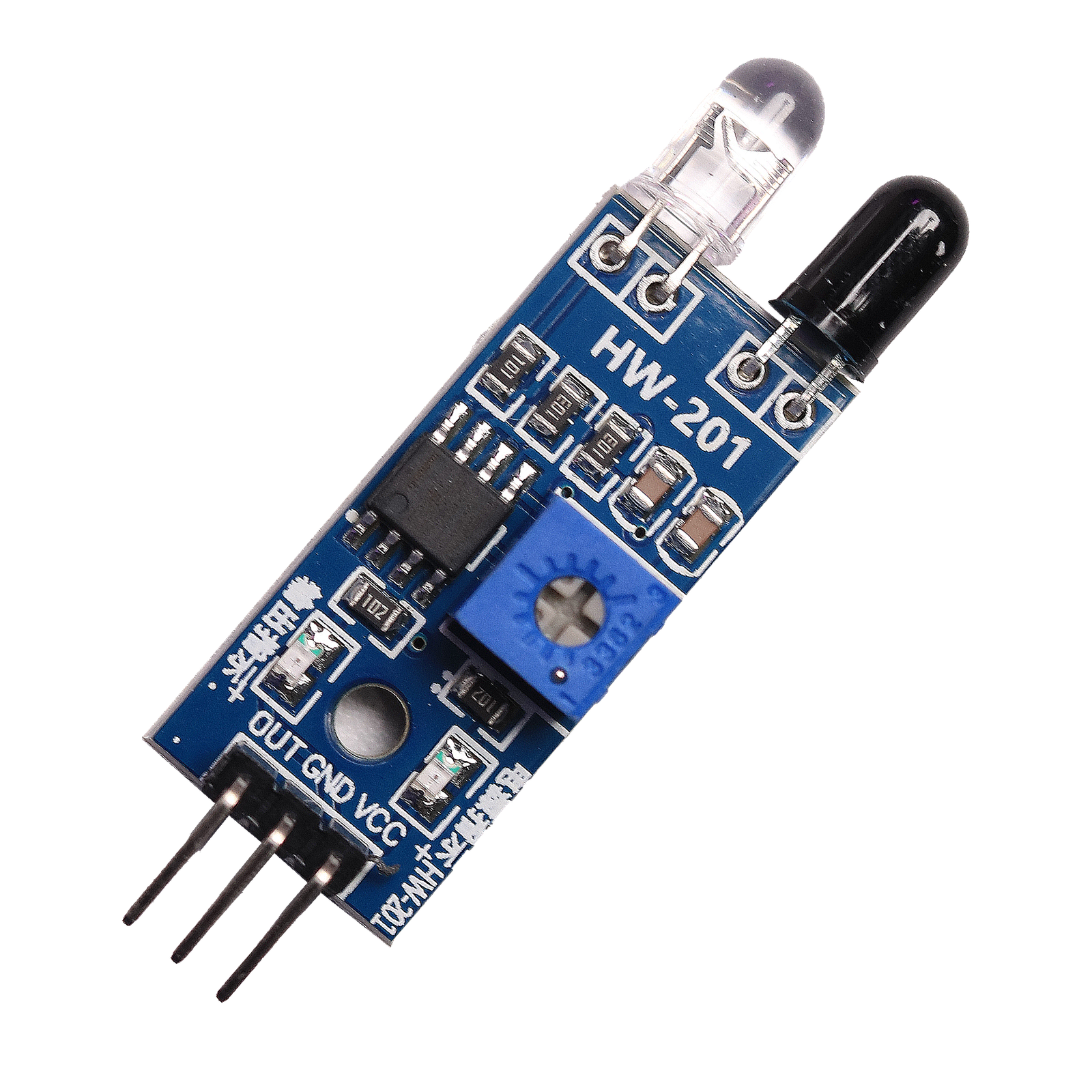