Cool Info About What Is The Difference Between Star And Delta Wiring
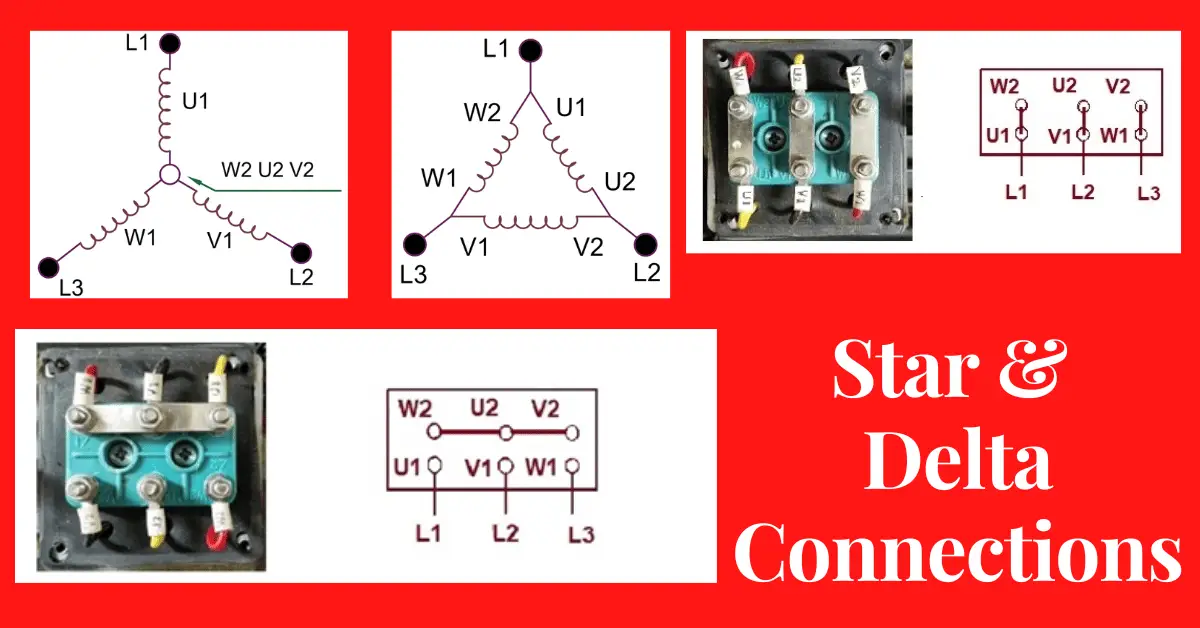
How To Connect A 3 Phase Motor In Star And Delta?
Star vs. Delta
1. Understanding the Basics
Ever wondered how electrical systems manage to power everything from your refrigerator to massive industrial machinery? A big part of that magic lies in how those systems are wired. Two common methods are star (also known as wye) and delta configurations. These aren't just fancy names; they're distinct wiring setups that impact voltage, current, and overall system performance. Think of it like choosing between a pickup truck for heavy-duty hauling (delta) or a fuel-efficient sedan for everyday use (star). Each has its strengths!
The crucial keyword here is, of course, star and delta wiring (noun). That's the core of what we're diving into. It's the foundation upon which much of our understanding will be built.
Let's imagine electricity flowing like water through pipes. In a star connection, all the pipes (or rather, the phases) meet at a central point, like tributaries flowing into a lake. In a delta connection, the pipes form a closed loop, a continuous circuit without a central point. This seemingly small difference has major implications for how the electrical system behaves.
Essentially, the choice between star and delta often comes down to the application. Do you need high starting torque for a motor, or a stable voltage for sensitive equipment? These are the kinds of questions electrical engineers consider when designing power distribution systems.
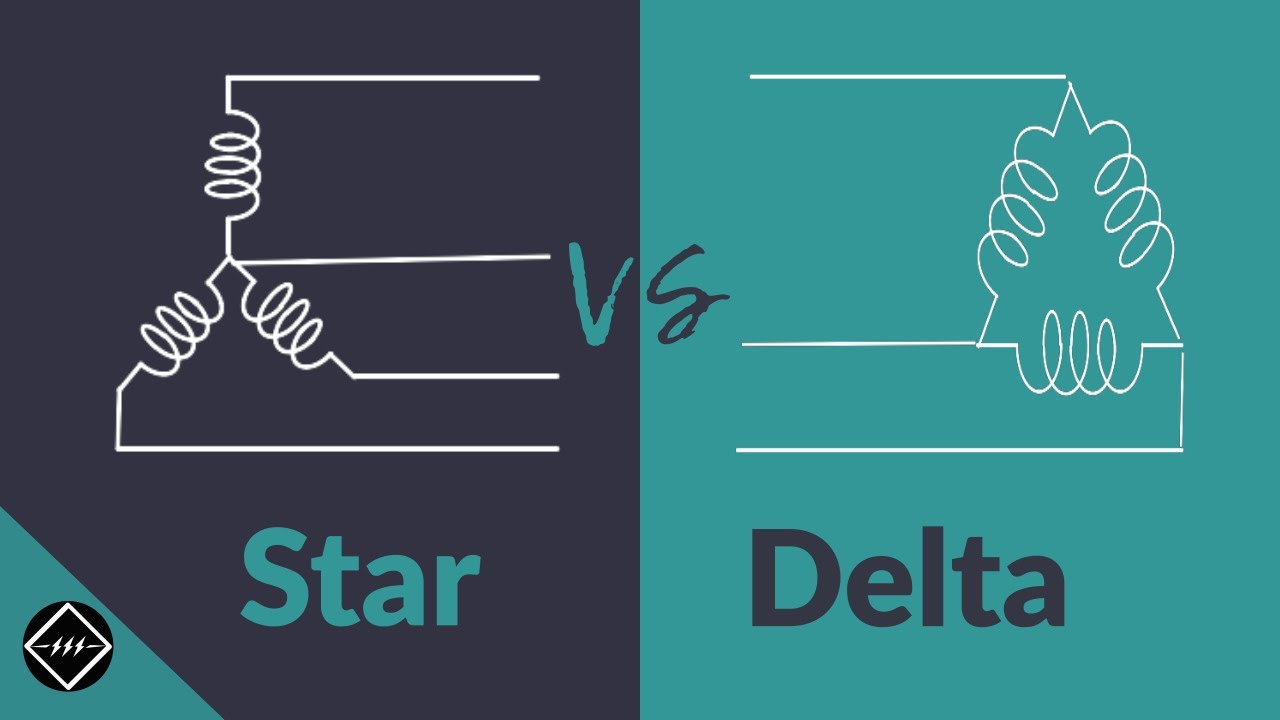
The Star Connection
2. Digging Deeper into Star (Wye) Wiring
In a star or wye connection, three windings (think of them as coils of wire) are connected at a common neutral point. This neutral point is usually grounded, providing a return path for current and a reference point for voltage measurements. It's a bit like having a safety net in case something goes wrong.
One of the main advantages of a star connection is that it provides two voltage levels: a phase-to-neutral voltage (the voltage between one of the phases and the neutral point) and a phase-to-phase voltage (the voltage between any two phases). The phase-to-phase voltage is typically 3 (approximately 1.732) times the phase-to-neutral voltage. This flexibility makes star connections suitable for a wide range of applications, from powering household appliances to supplying industrial loads.
Think about your home's electrical panel. It likely uses a star connection to provide both 120V outlets (phase-to-neutral) and 240V outlets (phase-to-phase) for larger appliances like dryers and ovens. It's a clever way to get the most out of a single electrical supply.
Star connections are also known for their good voltage regulation, meaning that the voltage remains relatively stable even under varying load conditions. This is important for sensitive electronic equipment that can be damaged by voltage fluctuations. It's like having a smooth, steady power supply instead of a bumpy, unpredictable one.
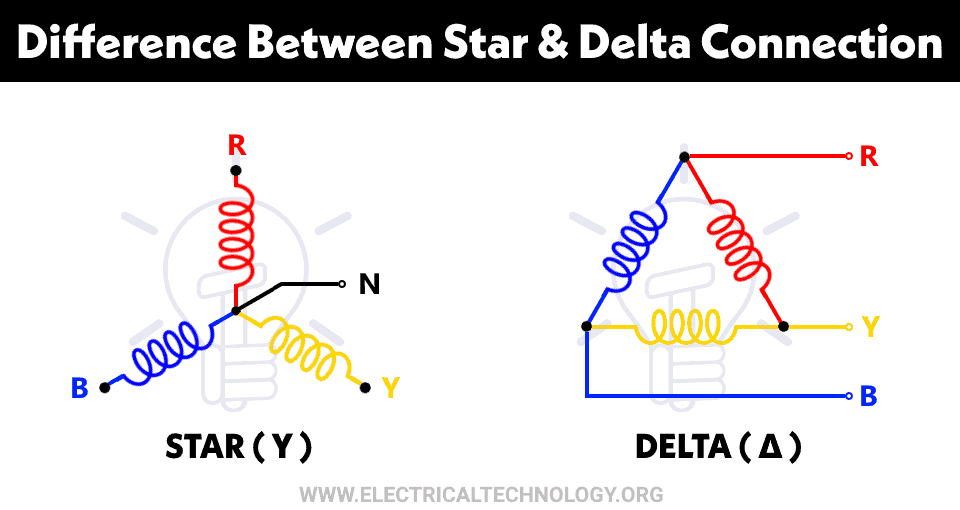
Delta Connection
3. Exploring the Characteristics of Delta Wiring
Now, let's shift our focus to the delta connection. Unlike the star connection, the three windings in a delta connection are connected in a closed loop, forming a triangle (hence the name "delta," which resembles the Greek letter ). There's no neutral point in a standard delta configuration. This means there's only one voltage level available: the phase-to-phase voltage.
Delta connections are often used in applications where high starting torque is required, such as powering large motors. The closed-loop configuration allows for a higher circulating current during startup, which provides the necessary oomph to get the motor running. It's like giving the motor a powerful initial push.
However, delta connections are generally more susceptible to voltage imbalances than star connections. If one phase experiences a voltage drop, it can affect the entire system. This is because the voltage is directly coupled between the phases in the closed loop.
Because there is no neutral in a standard delta, single-phase loads cannot be supplied directly. A workaround is to use a "corner grounded delta" configuration. This involves grounding one of the phase conductors. While this can allow for some single-phase usage, it also creates other complications and is generally avoided unless specifically needed.
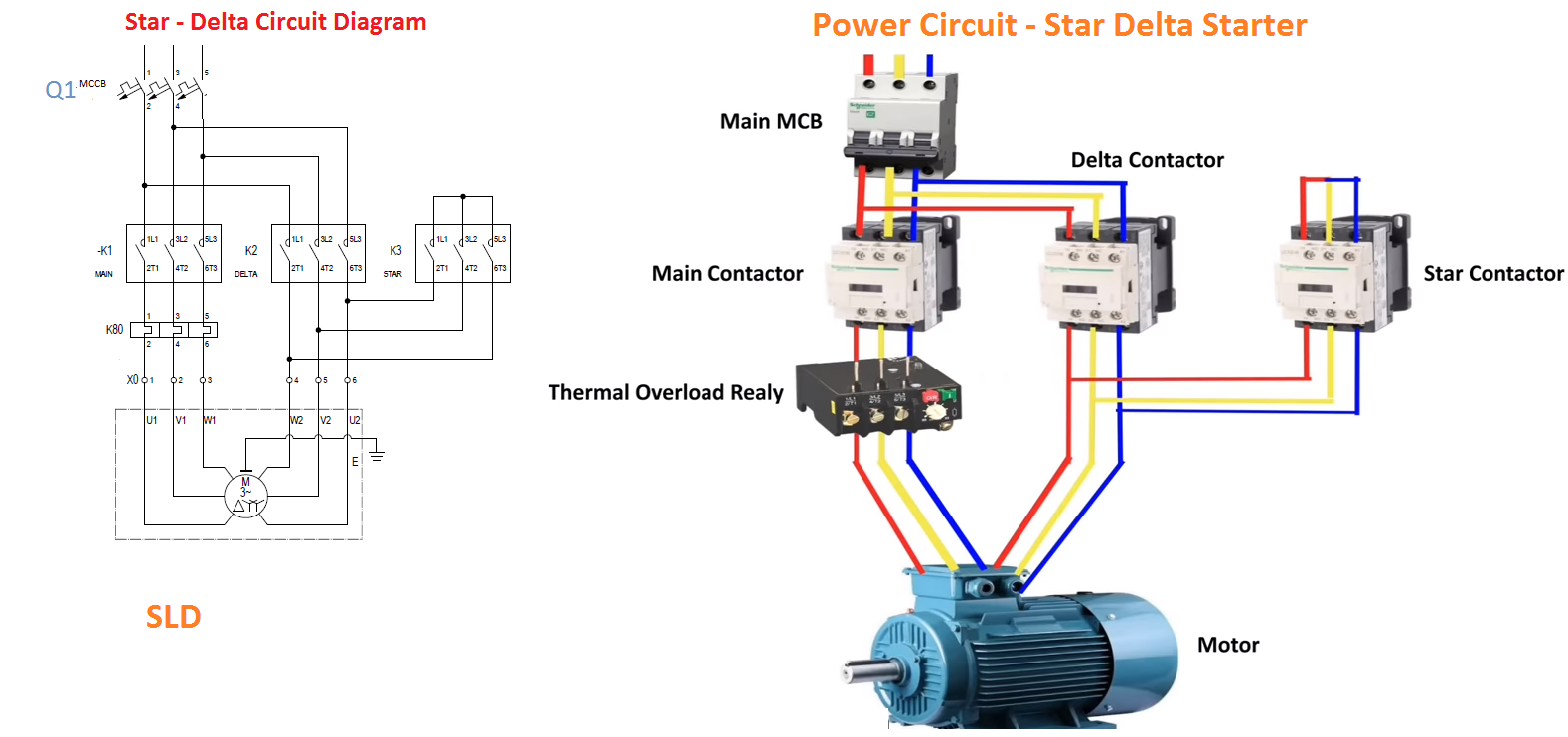
Star Delta Wiring Explained
Key Differences Summarized
4. Star vs. Delta
To recap, the main differences between star and delta wiring are:
Neutral Point: Star connections have a neutral point, while delta connections typically don't.
Voltage Levels: Star connections offer two voltage levels (phase-to-neutral and phase-to-phase), while delta connections offer only one (phase-to-phase).
Starting Torque: Delta connections generally provide higher starting torque for motors.
Voltage Balance: Star connections are generally more stable under voltage imbalances.
Single Phase Loads Star connections can easily handle single phase loads.Choosing between star and delta wiring involves a careful consideration of these factors, as well as other application-specific requirements. It's a balancing act between voltage levels, torque requirements, and system stability.
It's important to consult with qualified electrical professionals when designing or modifying electrical systems. They can assess your specific needs and recommend the most appropriate wiring configuration for your application.
So, next time you see a motor roaring to life or your lights shining brightly, remember that star and delta wiring are working hard behind the scenes to make it all possible!
Applications in the Real World
5. Where You'll Find Star and Delta Setups
Star connections are commonly used in power distribution networks to supply residential and commercial buildings. The availability of two voltage levels makes them ideal for powering a variety of loads, from lighting and appliances to office equipment. Think of your local power grid; chances are it uses a star configuration for the final distribution to your neighborhood.
Delta connections, on the other hand, are often used in industrial applications to power large motors and other heavy-duty equipment. The high starting torque provided by delta connections is essential for these types of applications.
In some cases, a combination of star and delta connections may be used in the same system. For example, a motor may be started in a delta configuration to provide high starting torque and then switched to a star configuration for running at normal speed. This is known as star-delta starting, and it's a common technique for reducing the inrush current during motor startup.
You might find delta setups in specialized machinery and large manufacturing plants. The specific needs of the equipment and the desired performance characteristics dictate the choice.
FAQs About Star and Delta Wiring
6. Your Burning Questions Answered
Let's tackle some frequently asked questions about star and delta wiring:
Q: Can I convert a star connection to a delta connection, or vice versa?
A: Yes, it's theoretically* possible, but it usually requires rewinding the transformer or motor windings. It's not a simple task and should only be done by qualified professionals.
Q: Is one connection inherently better than the other?
A: Nope! It depends entirely on the application. Each connection has its own strengths and weaknesses.
Q: What happens if I connect a 240V appliance to a 120V outlet?
A: Bad things! You'll likely damage the appliance and potentially cause a fire. Always make sure the voltage matches the appliance's requirements.
Q: Are Star and Wye connections the same?
A: Yes! Star and Wye are interchangable terms for the same type of electrical connection.
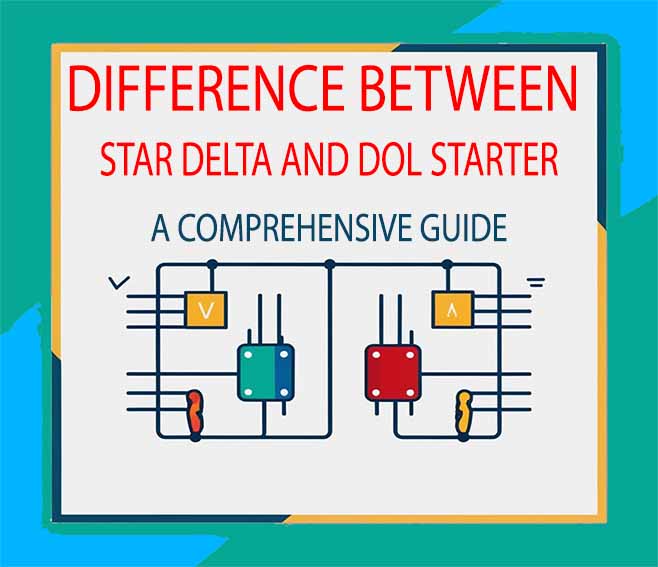