Nice Tips About How To Torque Without A Wrench
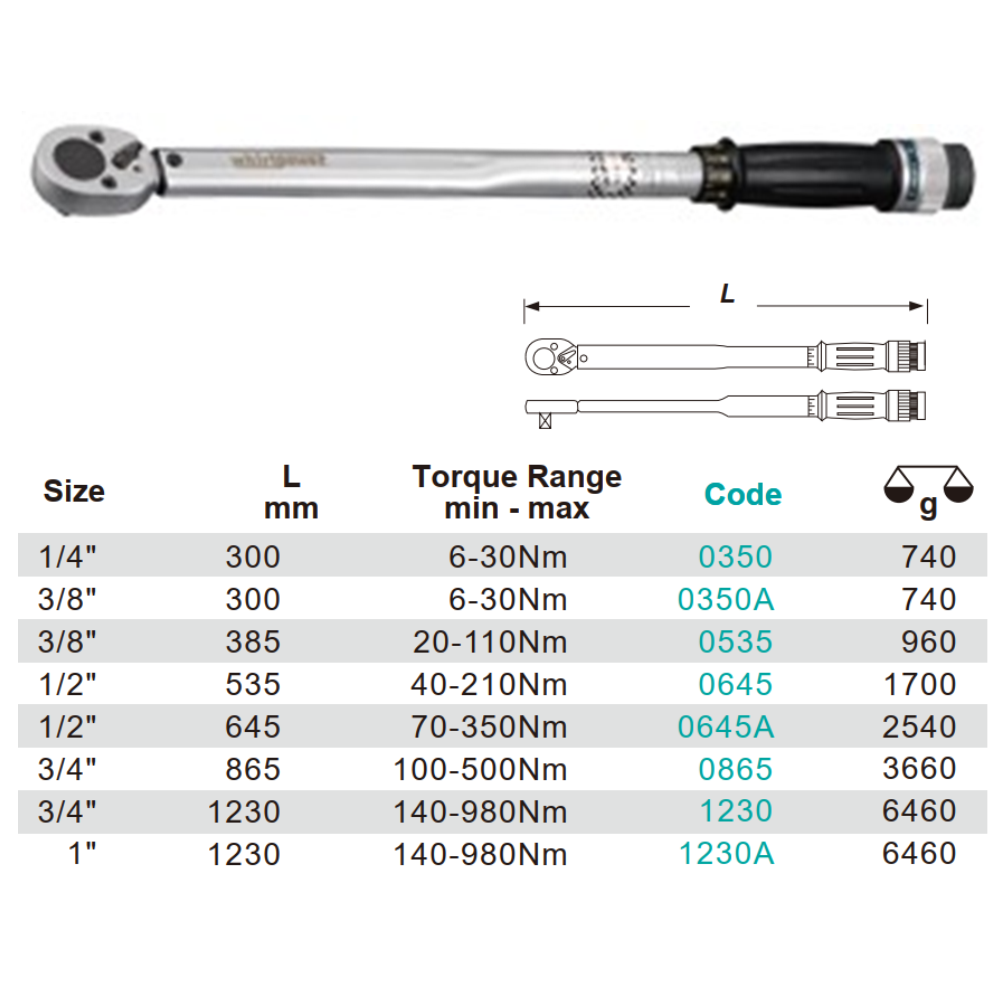
Torquing Troubles? No Torque Wrench, No Problem!
1. The Quest for Tightening Just Right
Alright, let's face it. We've all been there. You're elbows-deep in a project, ready to button everything up, and BAM! You realize your trusty torque wrench is MIA. Maybe it's borrowed, lost in the abyss of your garage, or perhaps you never even owned one to begin with. Don't panic! Before you resign yourself to over-tightening and stripping threads (we've all been there, right?), let's explore some clever workarounds for "how to torque without a torque wrench". Because sometimes, ingenuity is the best tool in the box.
Now, before we dive in, let's be crystal clear: nothing beats the precision of a properly calibrated torque wrench. If accuracy is absolutely critical (think engine internals or safety-sensitive components), borrowing, renting, or buying a torque wrench is the way to go. But for those less critical situations, these methods can get you surprisingly close.
The key is understanding what torque actually is. It's a rotational force, a measure of how much twisting power you're applying. Think of it like trying to open a stubborn jar. More torque means more effort to turn the lid. We're trying to estimate that twisting effort and control it.
So, buckle up! We're about to get resourceful and learn how to approximate torque with a little bit of math, a dash of feel, and a whole lot of common sense. Let's make sure your project stays together, without causing any mechanical mayhem.
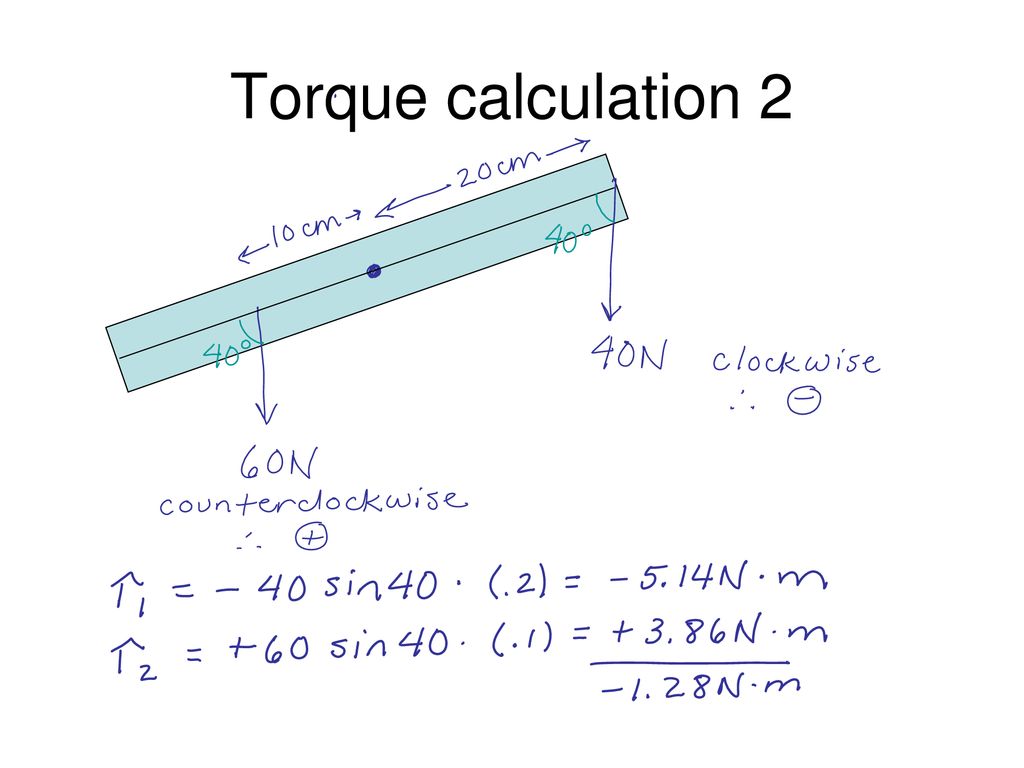
Torque Wrench. Ppt Download
Method 1
2. Leveraging Leverage and Angles
This method relies on understanding leverage and applying a calculated force. It's a bit more involved than just winging it, but it offers a decent level of accuracy if you're careful. It basically uses your wrench and arm as a lever to apply a calculated weight and force.
First, you need to know the required torque value for the bolt or nut you're working with. This is usually found in the service manual or specifications for your project. Let's say it's 30 foot-pounds (ft-lbs) for our example. Next, measure the length of your wrench from the center of the bolt to where you'll apply force with your hand (in feet). Let's say it's 1 foot.
Now, do some simple math: Torque (ft-lbs) = Force (lbs) x Length (ft). To find the force you need to apply, rearrange the equation: Force (lbs) = Torque (ft-lbs) / Length (ft). In our example: Force = 30 ft-lbs / 1 ft = 30 lbs. So, you need to apply 30 pounds of force to the end of your wrench.
Here's the tricky part: estimating 30 pounds of force. The easiest way is to use a bathroom scale. Hold the wrench horizontally and position it so the end rests on the scale. Push down until the scale reads 30 pounds. Get a feel for how much effort that takes. Now, transfer that same feeling to tightening the bolt, using the "clock-face" method — visualize the nut as a clock face and tighten in small, controlled increments.
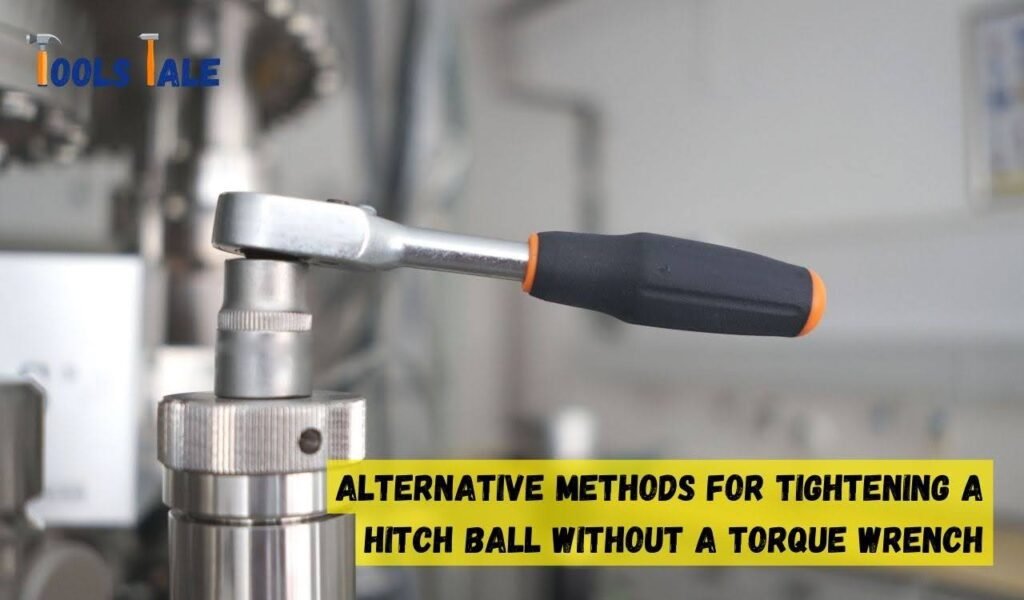
A Guide On How To Tighten Hitch Ball Without Torque Wrench
Method 2
3. Honing Your Inner Torque Wrench
This method is more art than science, and it relies heavily on experience. It's basically developing a sense for how tight is tight enough, but it's not for beginners. Its the skill that separates the weekend warrior from the seasoned pro.
The "feel" method involves paying close attention to the resistance you encounter as you tighten the bolt or nut. You're looking for a gradual increase in resistance, followed by a point where it becomes significantly harder to turn. The key is to stop just before that point. Over-tightening is a common mistake that leads to stripped threads and broken bolts.
Start by snugging the bolt or nut down gently. Then, gradually increase the tightening force, paying attention to how the wrench feels in your hand. Look for visual cues, such as the compression of a washer or the slight deformation of a gasket. These can be indicators that you're reaching the desired torque.
Remember, this method requires a good understanding of the materials you're working with and the specific application. The torque required for a small bolt in plastic will be vastly different from the torque required for a large bolt in steel. Start with lighter pressure, and then slowly increase it until you feel resistance. If you doubt, just dont!

Is Your Torque Wrench Accurate? How To Test Or Calibrate
Method 3
4. A Simple Rotation for a Solid Fastening
This technique relies on tightening the nut a specific amount after it's already snug. It's surprisingly effective, particularly for certain applications like head bolts or wheel bearings where controlled stretching of the bolt is crucial.
First, snug the nut down until it's just contacting the surface. This is "zero" position. Now, refer to the manufacturer's specifications for the required "turn of the nut." This is usually expressed in degrees, such as "90 degrees" or "180 degrees."
Using a marker, draw a line on the nut and a corresponding line on the surface it's tightening against. This will serve as your visual reference. Now, turn the nut the specified number of degrees, aligning the line on the nut with the appropriate mark on the surface. For example, 90 degrees is a quarter-turn, and 180 degrees is a half-turn.
This method is particularly effective for fasteners that are designed to stretch slightly when tightened, creating a strong and reliable clamping force. However, it's crucial to consult the manufacturer's specifications to ensure you're using the correct turn angle. Over-rotating can damage the fastener or the components being joined.
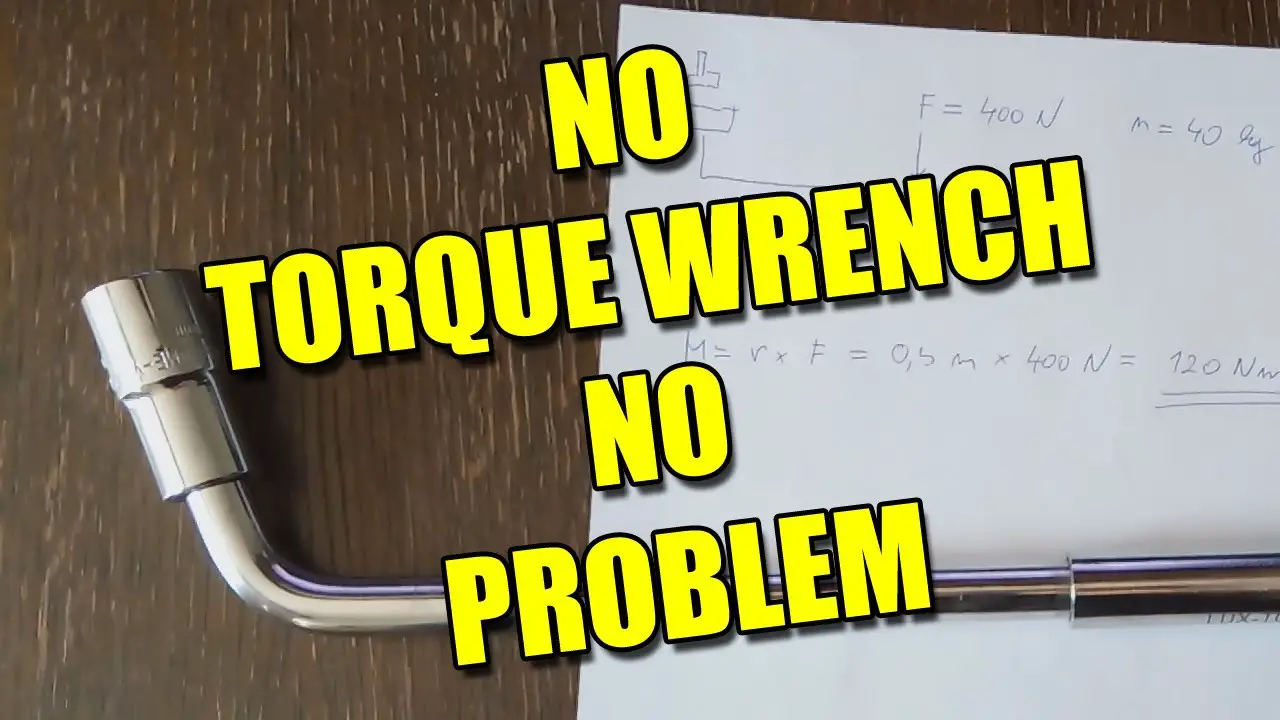
How To Properly Torque A Bolt Without Wrench
Important Considerations and Caveats
5. Safety First, Always!
No matter which method you choose, safety should always be your top priority. Always wear safety glasses to protect your eyes from flying debris. Make sure the bolt or nut is properly seated and that the threads are clean and undamaged. Using a damaged or improperly seated fastener can lead to inaccurate torque and potential failure.
Also, remember that these methods are approximations. They're not as accurate as using a torque wrench, so they should only be used in situations where precision is not critical. If you're working on a safety-sensitive component, such as brakes or suspension, always use a torque wrench and follow the manufacturer's specifications.
Lubrication plays a crucial role in torque. If the threads are dry, the friction will be higher, and you'll end up over-tightening the fastener. Always lubricate the threads with a suitable lubricant, such as anti-seize compound or oil, unless otherwise specified by the manufacturer.
And finally, always double-check your work. After tightening the bolt or nut, visually inspect it to make sure it's properly seated and that there are no signs of damage. If you're unsure, it's always better to err on the side of caution and re-tighten the fastener using a torque wrench.

How To Torque Without A Wrench Mastering The Art Of Precision
FAQ
6. Frequently Asked Questions
Q: Can I really get away with not using a torque wrench?A: In a pinch, yes, for less critical applications. But for anything involving safety (brakes, suspension, engine internals), a torque wrench is a must. Think of it like this: would you rather spend a little extra time and money to do it right, or risk a major malfunction down the road?
Q: What if I strip the threads?A: Stripped threads are a nightmare. If you suspect you've stripped the threads, stop immediately. Trying to force the bolt or nut further will only make things worse. You may need to repair the threads using a thread repair kit or replace the damaged component. Prevention is better than cure — use a torque wrench, or be extra careful with the methods above.
Q: Is there a universal "feel" for tightening bolts?A: Unfortunately, no. The "feel" varies depending on the size of the bolt, the material it's made of, and the application. That's why experience is so important when using the "feel" method. The more you work on different types of projects, the better you'll become at judging the correct torque.
Q: What about using a cheater bar to increase leverage?A: While tempting, using a cheater bar without a torque wrench is a recipe for disaster. You'll have absolutely no control over the torque, and you're highly likely to over-tighten the fastener and strip the threads or break the bolt. Avoid cheater bars unless you absolutely know what you're doing AND have a calibrated torque wrench.