Beautiful Info About Why Do We Use Torque Settings
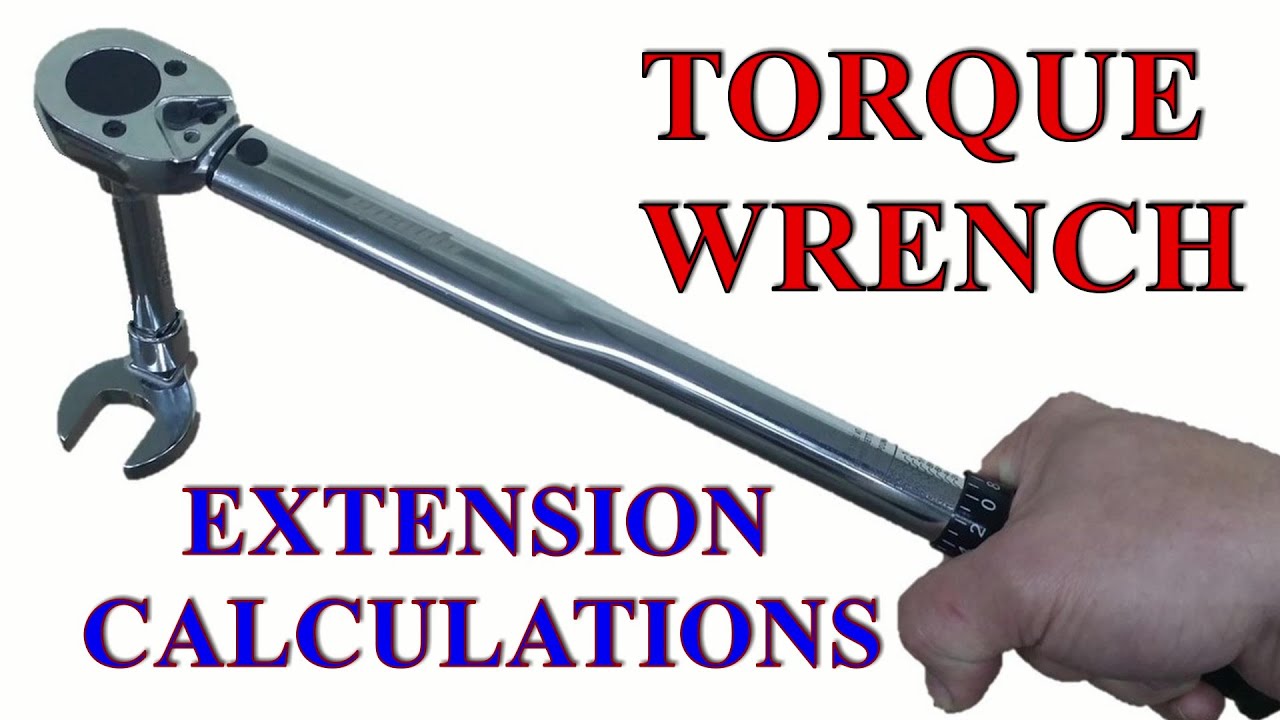
Why Do We Use Torque Settings? A Slightly-More-Than-You-Bargained-For Explanation
1. The Mystery of the Tightening Torque
Ever wondered why your mechanic is so obsessed with torque wrenches? It's not just a random act of tool worship, I promise! Using torque settings is crucial for a bunch of reasons, all boiling down to making sure things are both secure and not broken. Think of it like Goldilocks and the Three Bears, but instead of porridge, it's nuts and bolts. Too loose, and things fall apart. Too tight, and well, let's just say things get messy.
Seriously, improperly tightened fasteners can lead to some seriously unwanted consequences. Imagine a wheel coming loose on your car while you're driving down the highway. Not a pleasant thought, right? Or perhaps a critical engine component failing because it wasn't properly secured. These aren't just theoretical scenarios; they're real risks that torque settings help to prevent. That precise click of a torque wrench isnt just satisfying; it's a small act of mechanical heroism, ensuring your safety and the longevity of your equipment.
The key is achieving the right amount of clamping force. Thats the force that presses the joined parts together. Torque settings provide a standardized way to achieve this, taking into account factors like bolt size, material, and thread pitch. Without a torque setting, we're just guessing, which is rarely a good strategy when dealing with machinery. And trust me, guessing wrong with bolts can be a significantly expensive mistake. Think about how much it would cost to fix or replace broken parts.
So, really, using torque settings is all about precision and control. It's about making sure that every bolt and nut is tightened to the optimal level, preventing both loosening and over-stressing. In the world of mechanics and engineering, that precision can make all the difference between a smoothly running machine and a catastrophic failure. It's the peace of mind that comes from knowing things are done right, down to the tiniest detail. The "why" boils down to safety, reliability, and avoiding very expensive mistakes.

Torque Specifications For Electrical Connections At Meagan Burlingame Blog
The Downside of Guesswork
2. The Problem with Just Winging It
Okay, I get it. Some of you seasoned veterans out there might be thinking, "I've been tightening bolts by feel for years, and I've never had a problem!" While experience definitely counts for something, relying solely on "feel" can be a risky game. Every bolt is different, every application is different, and even the strongest mechanic's grip can vary depending on how much coffee they've had that morning. Our feelings aren't standardized tools for consistent results, like torque wrenches.
Here's the thing: our sense of "tight enough" can be easily fooled. We might over-tighten a bolt, stretching it beyond its yield strength. This weakens the bolt, making it more likely to fail under stress. Or, we might under-tighten it, leaving it vulnerable to loosening due to vibration or thermal expansion. Either way, we're setting ourselves up for potential problems down the line. In either scenario you can still feel as though you tightened something with the proper torque.
Furthermore, "feel" doesn't account for factors like lubrication. A lubricated bolt will require less torque to achieve the same clamping force as a dry bolt. Ignoring this can lead to over-tightening and potential damage. Torque settings, on the other hand, often specify whether the bolt should be lubricated and provide adjusted torque values accordingly. That is a huge consideration in the overall process of tightening bolts properly.
Think of it like baking. Could you bake a cake by just "feeling" how much flour and sugar to add? Maybe, but it's unlikely to be as consistent or delicious as one made with precise measurements. Torque settings are the recipe for success when it comes to tightening fasteners. They provide a repeatable and reliable method for achieving the desired clamping force, regardless of the mechanic's mood or the weather outside. So, while experience is valuable, it's best paired with the precision of torque settings to ensure a job well done. After all, who wants a lopsided, burnt cake... or a loose wheel?
![[DIAGRAM] Pneumatic Torque Wrench Diagram [DIAGRAM] Pneumatic Torque Wrench Diagram](https://fthmb.tqn.com/70dOwigiDy7byopL29XqtOBoXHI=/768x0/filters:no_upscale()/Direct_pawl_clicker_torque_concept-59b031c9519de20010ef9888.png)
The Right Tool for the Job
3. Torque Wrenches
So, we've established that torque settings are important. But how do we actually achieve them? That's where torque wrenches come in. These specialized tools are designed to measure and apply a specific amount of torque to a fastener. There are several different types of torque wrenches, each with its own strengths and weaknesses, but they all share the same basic goal: to provide precise control over tightening.
The most common type of torque wrench is the click-type wrench. This wrench has a mechanism that releases with an audible "click" when the desired torque is reached. It's relatively easy to use and provides a clear indication of when to stop tightening. There are also beam-type wrenches, which use a pointer and scale to indicate the torque being applied. These are generally less expensive but require more visual attention.
Electronic torque wrenches are another option, offering digital displays and programmable torque settings. These are often used in high-precision applications where accuracy is paramount. Regardless of the type, it's crucial to calibrate your torque wrench regularly to ensure its accuracy. A torque wrench that's out of calibration is worse than no torque wrench at all, as it can give you a false sense of security.
Choosing the right torque wrench for the job depends on several factors, including the torque range required, the accessibility of the fastener, and your budget. A small, low-torque wrench might be suitable for tightening delicate components, while a larger, high-torque wrench is needed for heavy-duty applications. The right torque wrench, properly calibrated and used correctly, is your best friend when it comes to achieving accurate and reliable tightening. It's an investment in safety, reliability, and the longevity of your equipment. So, treat it well!
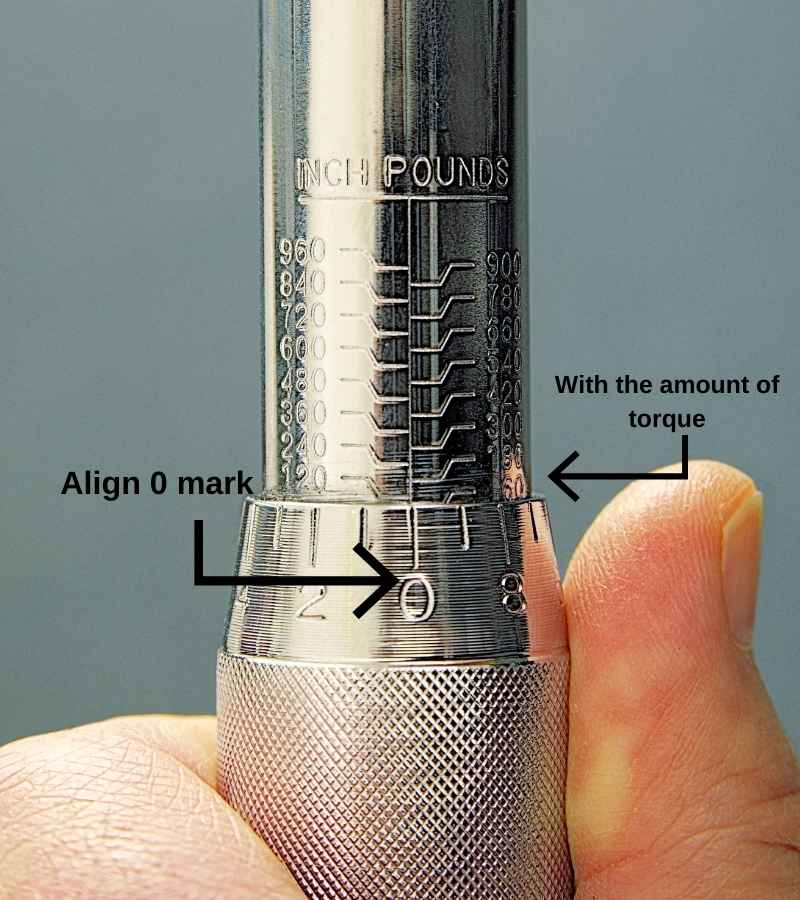
Where to Find Torque Settings (Because Nobody Knows Everything)
4. The Quest for Correct Torque Specifications
Alright, you're convinced. Torque settings are important, and you have a fancy torque wrench. Now comes the million-dollar question: where do you find the correct torque setting for a particular bolt or nut? Fortunately, there are several reliable sources of information available. Because tightening something to any random torque isn't going to get you very far in the goal of things staying together.
The most common source is the vehicle or equipment manufacturer's service manual. These manuals typically provide detailed torque specifications for every fastener on the machine. They may also include diagrams or illustrations to help you identify the correct bolt or nut. Another useful resource is online torque charts, which provide general torque recommendations based on bolt size, material, and thread pitch. However, it's important to remember that these charts are only guidelines, and you should always refer to the manufacturer's service manual for the most accurate information. These charts are a fantastic way to get an idea of what torque values to expect.
For specialized applications, you may need to consult engineering standards or industry-specific guidelines. These documents often provide more detailed information about torque settings and other fastening requirements. If you're unsure about the correct torque setting, it's always best to err on the side of caution and consult a qualified mechanic or engineer. They can help you determine the appropriate torque value and ensure that the fastener is properly tightened. It's better to ask than to risk damage or failure.
Remember, torque settings are not one-size-fits-all. They vary depending on the application, bolt size, material, and other factors. Always consult a reliable source of information before tightening any fastener, and never guess! Taking the time to find the correct torque setting can save you a lot of headaches (and money) in the long run. Consider the cost of doing it wrong versus the small amount of time to find the proper specification. It's an easy choice.
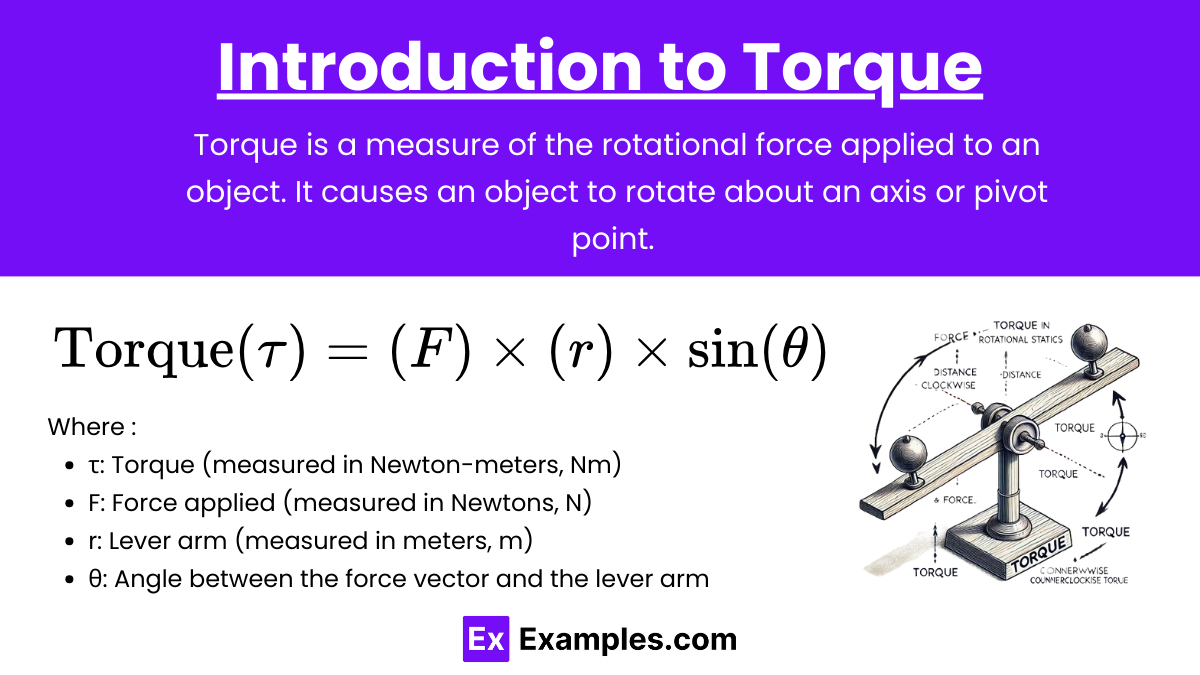
In conclusion, Torque Settings
5. Why the Fuss? Because It Matters.
So, why do we use torque settings? It's simple: because they matter. They're not just arbitrary numbers plucked from thin air; they're carefully calculated values that ensure the safety, reliability, and longevity of our machines and equipment. Using torque settings is a small act of precision that can have a big impact, preventing everything from loose wheels to catastrophic engine failures. It's a commitment to doing things right, down to the smallest detail.
While experience and "feel" can be valuable, they should never be relied upon as a substitute for accurate torque settings. Torque wrenches are essential tools for achieving the desired clamping force, and they should be used and maintained properly. Remember to consult reliable sources of information to find the correct torque setting for each application, and never guess! Because as we talked about, it's easy to feel you have tightened something with a certain torque, when in reality, you have not.
Think of torque settings as the unsung heroes of the mechanical world. They're not always glamorous, but they play a vital role in keeping things running smoothly and safely. So, the next time you reach for a torque wrench, remember the importance of what you're doing. You're not just tightening a bolt; you're ensuring the integrity of a system, protecting yourself and others, and contributing to a world where things stay together the way they're supposed to. And isn't that a worthy goal? Yes, yes it is.
From car engines to bicycles, torque settings are everywhere. They are a foundational component to many applications, and a good understanding of why they are important can help to prevent mechanical failure, which can cause injury to people or expensive repairs. We hope that this article has helped provide a foundational understanding of why we use torque settings. They really do matter.
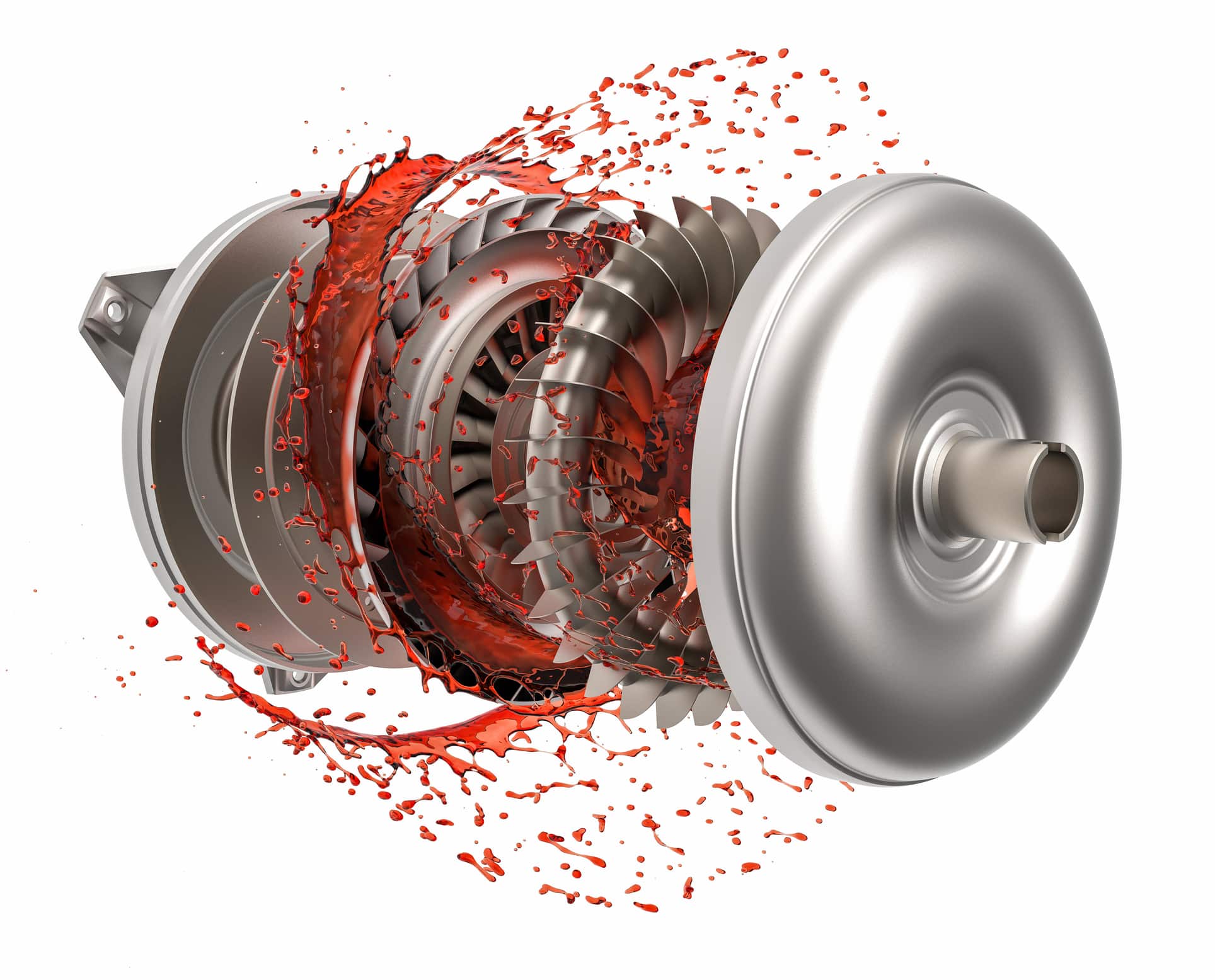
Frequently Asked Questions (FAQ)
6. Question 1
Over-tightening a bolt can stretch it beyond its yield strength, weakening it and making it more likely to fail under stress. It can also damage the threads on the bolt or the mating component, leading to costly repairs. In some cases, it can even cause the bolt to snap, creating a dangerous situation.
7. Question 2
It's generally recommended to calibrate your torque wrench at least once a year, or more frequently if you use it heavily or suspect it may be out of calibration. Calibration ensures that the wrench is accurately measuring torque, preventing over- or under-tightening.
8. Question 3
No, a regular wrench cannot be used to accurately tighten a bolt to a specific torque setting. Regular wrenches do not have a mechanism for measuring torque, so you would be relying solely on guesswork, which can lead to inaccurate and potentially dangerous results. Always use a torque wrench to achieve the desired clamping force.