Outrageous Tips About How To Use A Torque Device

Torque Wrench Calibration Tester At Bambi Foust Blog
Understanding Torque and Why It Matters
1. What Exactly is Torque, Anyway?
Okay, let's dive straight in. Torque, in simple terms, is a twisting force that causes rotation. Think of it like the muscle you need to tighten a bolt or loosen a stubborn screw. It's not just about how hard you push or pull, but also where you apply that force. A longer wrench gives you more leverage, right? That's torque in action! It's a crucial factor in ensuring everything is fastened securely and doesn't fall apart, especially in machines and vehicles.
Imagine building a Lego castle. If you don't quite snap those bricks together firmly, it's going to wobble and eventually collapse. Torque is the Lego-snapping equivalent in the real world of mechanics and engineering. It makes sure things stay together, performing their function properly and, most importantly, safely.
So why is this twisting force so critical? Because insufficient torque can lead to loose connections, which translates to vibrations, leaks, and eventual failure. Over-torque, on the other hand, can strip threads, snap bolts, and damage components. Neither scenario is desirable, trust me! That's where a torque device comes into play, ensuring you apply just the right amount of force.
Think of it like Goldilocks and the Three Bears: you don't want too little, you don't want too much, you want it just right. Achieving that "just right" level of tightness requires precision, and thats exactly what torque devices offer.

What is a Torque Device ?
2. The Arsenal of Tools for Precision Tightening
Now that we know why torque is important, let's talk about how to control it. A torque device, at its core, is a tool designed to apply a specific amount of torque to a fastener. These tools come in various shapes and sizes, each tailored for different applications and torque ranges.
The most common type you'll encounter is the torque wrench. Picture it as a wrench with a built-in measuring device that tells you exactly how much twisting force you're applying. There are several types of torque wrenches, including click-type, beam-type, and digital ones, each offering its own set of pros and cons in terms of accuracy, ease of use, and cost.
Beyond wrenches, you'll also find torque screwdrivers for smaller, more delicate applications, and even specialized torque multipliers that amplify the force you apply, allowing you to tighten extremely large fasteners with relative ease. These tools aren't just for mechanics; they're used in manufacturing, construction, and even by DIY enthusiasts who want to ensure their projects are built to last.
Regardless of the specific tool, the underlying principle remains the same: to provide a controlled and measurable application of torque. They're indispensable for anyone working with machinery, engines, or anything where precise fastening is critical. So, gear up, because were about to dive into the usage techniques.

Prepping for the Task
3. Getting Ready to Torque
Before you even think about grabbing that torque device, a little preparation goes a long way. First and foremost, always refer to the manufacturer's specifications for the correct torque value for the fastener you're working with. This information is crucial and usually found in a repair manual, a parts diagram, or even stamped directly onto the component itself. Ignoring this step is like trying to bake a cake without a recipe you might end up with a disaster!
Next, inspect the fastener and the threads it's going into. Make sure everything is clean and free of debris. A little bit of dirt or rust can throw off your torque readings and lead to inaccurate tightening. If necessary, use a wire brush or thread chaser to clean things up. Applying a small amount of lubricant, especially on fasteners that will be exposed to the elements, can also help ensure smooth and accurate torque application.
Now, let's talk about the torque device itself. Before each use, inspect the tool for any signs of damage or wear. A damaged torque wrench can provide inaccurate readings and potentially lead to over- or under-tightening. If you're using a click-type torque wrench, make sure it's properly calibrated. Ideally, torque wrenches should be calibrated regularly, especially if they're used frequently.
Finally, ensure you have the correct socket or bit for the fastener you're working with. Using the wrong size can damage the fastener or the tool, and it's just plain frustrating. With a little bit of planning and preparation, you'll set yourself up for a successful and accurate torque application.
Home FUTEK Advanced Sensor Technology V2
The Actual Torqueing
4. Applying the Twist with Precision
Alright, you've got your torque specs, your clean fastener, and your trusty torque device ready to go. Now it's time to actually apply the torque. The first step is to adjust your torque device to the desired setting. For click-type torque wrenches, this usually involves rotating a handle or dial until the indicator aligns with the specified torque value. Make sure you understand how your specific torque device works before proceeding. Consulting the owner's manual is always a good idea.
Place the socket or bit onto the fastener and position the torque device so that you have a good, solid grip. Apply smooth, steady pressure to the torque device. Avoid jerky or rapid movements, as these can lead to inaccurate readings. As you apply pressure, listen carefully for the "click" (if you're using a click-type wrench) or watch the indicator (if you're using a beam-type or digital wrench). The goal is to reach the specified torque value without overshooting it.
Once you've reached the desired torque, stop applying pressure immediately. Overtightening can damage the fastener or the component it's holding together. If you're using a click-type wrench, the "click" indicates that you've reached the set torque. If you're using a beam-type wrench, the indicator should align with the specified value on the scale. Digital wrenches will typically beep or display a notification when the target torque is reached.
For some applications, especially those involving critical components, it's recommended to perform a final check. This involves repeating the torqueing process one or two more times to ensure that the fastener is properly tightened. Remember, consistency is key to achieving accurate and reliable torque application.
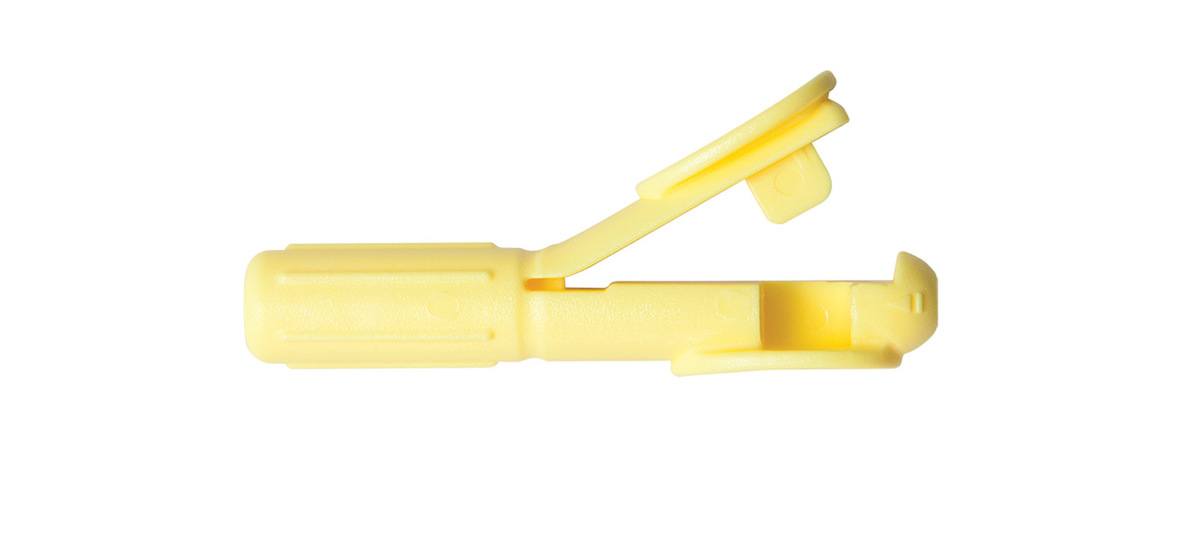
H2O Torq™ Torque Device Onehanded Manipulation Of The Guide Wire Tip
Post-Torqueing
5. Wrapping Up the Job the Right Way
You've applied the torque, heard the click (or seen the reading), and you're feeling pretty good. But the job isn't quite finished yet! Its wise to visually inspect the fastener and surrounding area. Make sure everything looks aligned and that there are no signs of damage or stress. If you notice anything unusual, it's worth investigating further.
After the torqueing process, be sure to reset your torque wrench to its lowest setting, especially if it's a click-type wrench. Leaving it set at a high torque value can damage the internal mechanism and affect its accuracy over time. Think of it like stretching a rubber band and leaving it stretched — it'll eventually lose its elasticity.
Finally, and this is often overlooked, properly store your torque device. Keep it in a clean, dry place, away from extreme temperatures or humidity. A good case or storage bag can help protect it from dust and damage. Taking care of your torque device will ensure that it remains accurate and reliable for years to come.
So, there you have it — a complete guide on how to use a torque device. Remember, precision is paramount when it comes to torque application. By following these steps and taking the time to do it right, you'll ensure that your fasteners are properly tightened, your equipment operates safely, and your projects stand the test of time. Now go forth and torque with confidence!
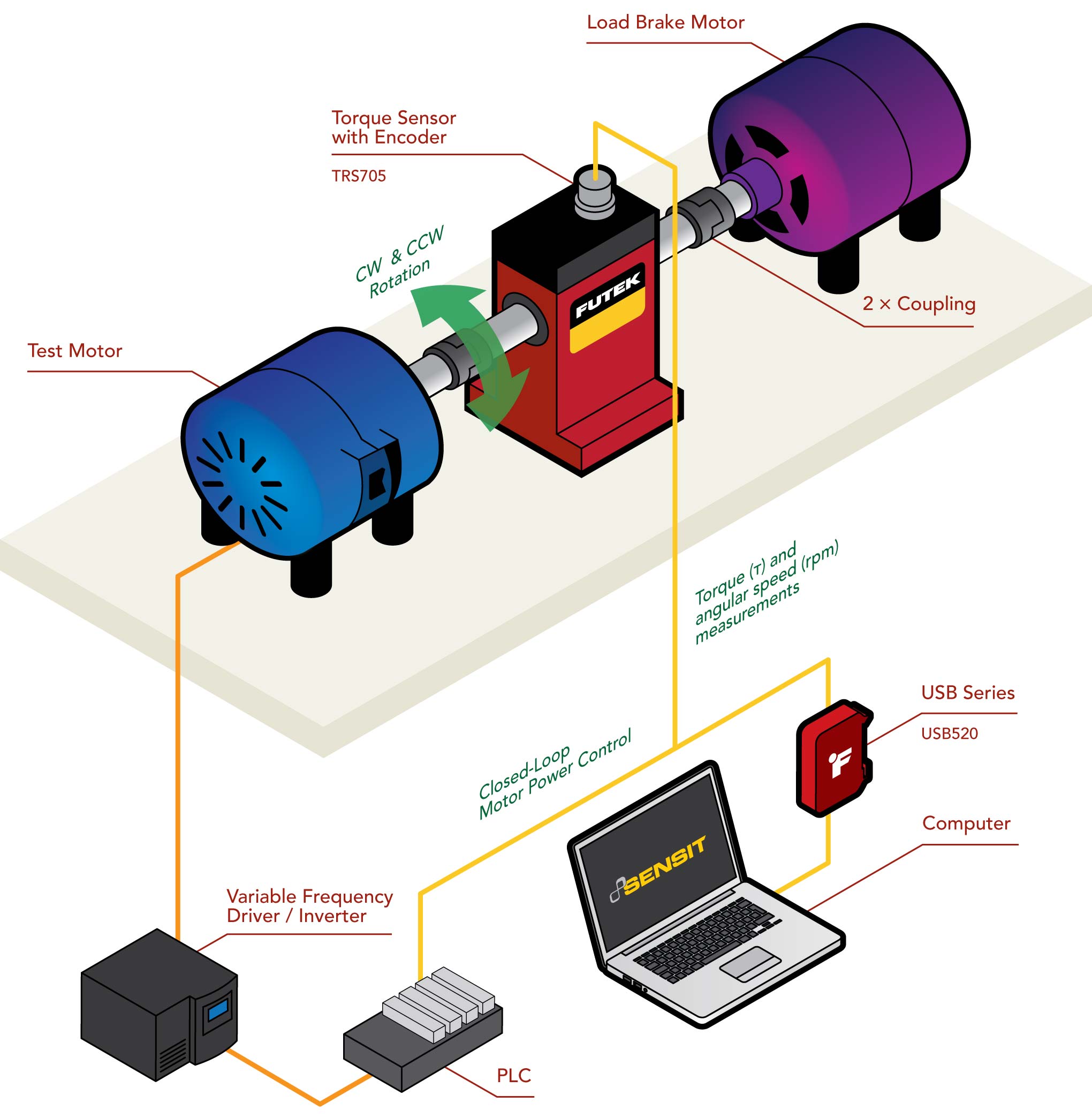
Torque Testing Methods At Jamie Spinelli Blog
Frequently Asked Questions (FAQs)
6. Your Burning Torque Questions, Answered!
Q: How often should I calibrate my torque wrench?A: It's generally recommended to calibrate your torque wrench every 5,000 uses or at least once a year, whichever comes first. If you use it frequently or expose it to harsh conditions, you might want to calibrate it more often.
Q: Can I use a torque wrench to loosen fasteners?A: While you can use a torque wrench to loosen fasteners, it's not recommended. Torque wrenches are designed for applying precise torque, and using them to loosen fasteners can damage the internal mechanism and affect their accuracy. It's better to use a regular wrench or breaker bar for loosening.
Q: What happens if I overtighten a fastener?A: Overtightening can strip the threads, snap the bolt, or damage the component being fastened. It's crucial to use the correct torque value and avoid applying excessive force.
Q: Are digital torque wrenches better than click-type?A: Both types have their pros and cons. Digital wrenches tend to be more accurate and offer features like data logging, but they're also more expensive and require batteries. Click-type wrenches are simpler, more durable, and don't require batteries, but they may not be as precise. The best choice depends on your specific needs and budget.